Alcast Company for Dummies
Alcast Company for Dummies
Blog Article
Alcast Company - Truths
Table of ContentsA Biased View of Alcast CompanyExcitement About Alcast CompanyThe Main Principles Of Alcast Company The 6-Minute Rule for Alcast CompanyGetting The Alcast Company To WorkGetting My Alcast Company To Work
Chemical Contrast of Cast Light weight aluminum Alloys Silicon promotes castability by minimizing the alloy's melting temperature level and improving fluidity throughout spreading. Furthermore, silicon contributes to the alloy's strength and use resistance, making it valuable in applications where toughness is important, such as automotive components and engine elements.It additionally boosts the machinability of the alloy, making it simpler to process into ended up products. In this method, iron adds to the total workability of light weight aluminum alloys.
Manganese contributes to the strength of aluminum alloys and boosts workability (aluminum metal casting). It is frequently utilized in wrought light weight aluminum items like sheets, extrusions, and profiles. The presence of manganese help in the alloy's formability and resistance to fracturing throughout construction procedures. Magnesium is a light-weight component that supplies stamina and influence resistance to aluminum alloys.
Some Known Details About Alcast Company
Zinc improves the castability of light weight aluminum alloys and aids control the solidification process throughout casting. It improves the alloy's toughness and solidity.
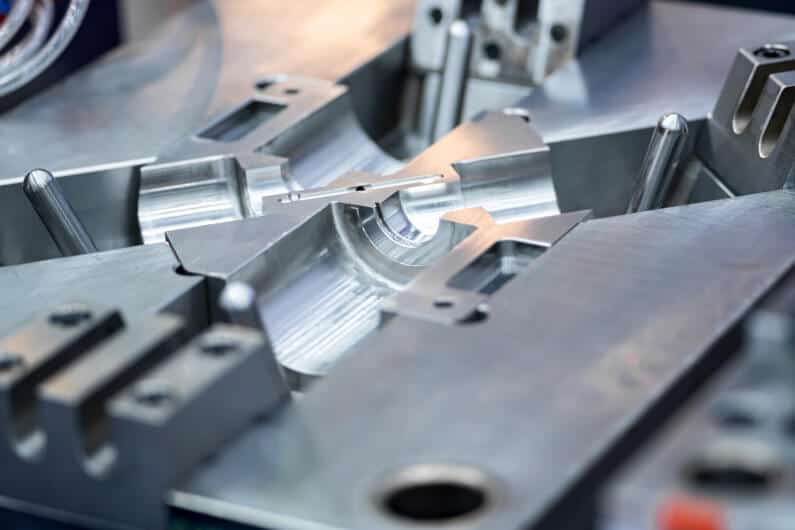
The main thermal conductivity, tensile strength, return toughness, and prolongation vary. Select appropriate raw products according to the performance of the target product produced. Among the above alloys, A356 has the highest possible thermal conductivity, and A380 and ADC12 have the cheapest. The tensile restriction is the contrary. A360 has the finest return strength and the greatest prolongation rate.
The 5-Second Trick For Alcast Company
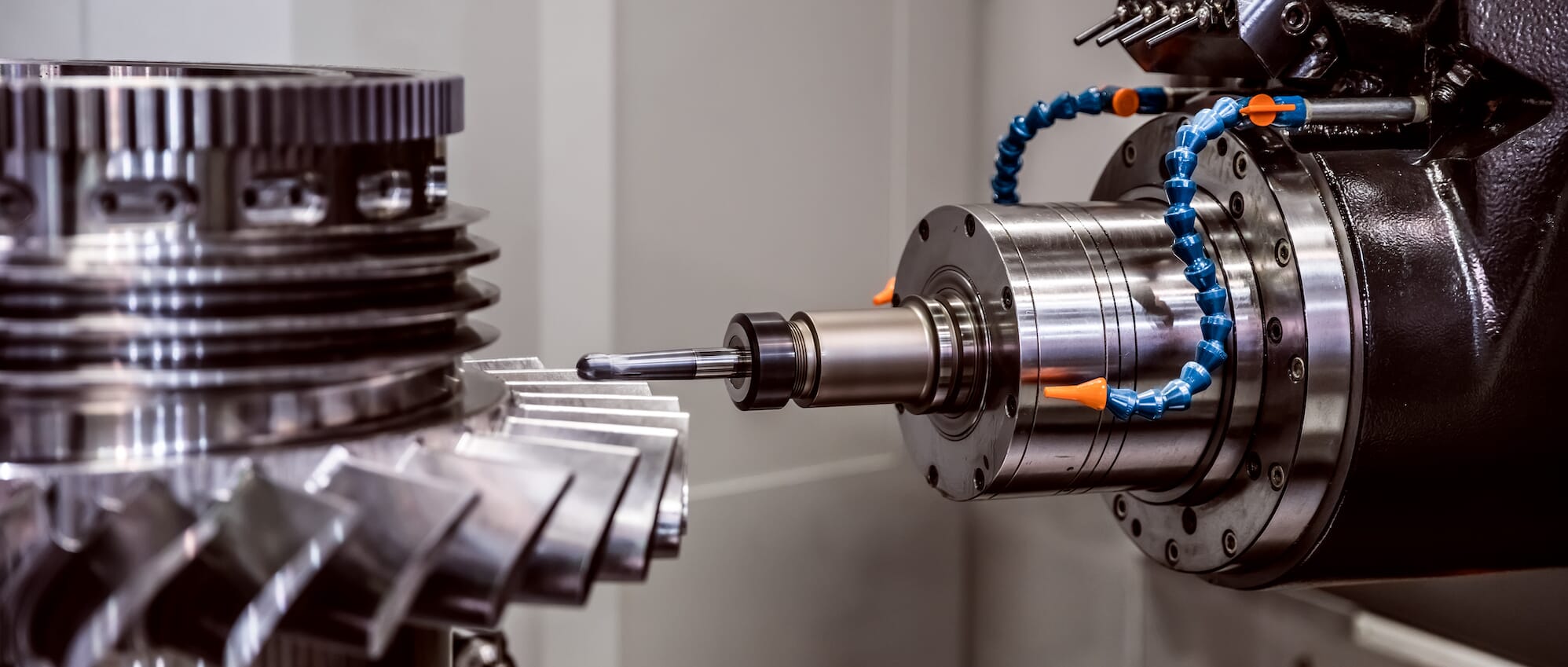
Its one-of-a-kind residential properties make A360 a beneficial choice for precision spreading in these industries, improving product sturdiness and quality. Light weight aluminum alloy 380, or A380, is an extensively used spreading alloy with a number of unique attributes. It offers exceptional castability, making it a suitable choice for accuracy casting. A380 shows good fluidity when molten, ensuring detailed and detailed molds are accurately replicated.
In precision spreading, light weight aluminum 413 beams in the Consumer Electronics and Power Devices sectors. This alloy's superior rust resistance makes it an excellent option for outdoor applications, guaranteeing lasting, long lasting products in the discussed industries.
The Greatest Guide To Alcast Company
The light weight aluminum alloy you select will substantially affect both the casting process and the properties of the last product. Because of this, you must make your decision very carefully and take an enlightened technique.
Establishing the most suitable light weight aluminum alloy for your application will imply considering a wide variety of features. These comparative alloy qualities follow the North American Die Spreading Association's standards, and we have actually separated them into two groups. The very first category addresses alloy qualities that influence the production procedure. The 2nd covers features influencing the buildings of the end product.
Excitement About Alcast Company
The alloy you select for die spreading straight impacts numerous facets of the spreading procedure, like exactly how very easy the alloy is to deal with and if it is prone to casting defects. Hot cracking, additionally understood as solidification splitting, is a typical die casting problem useful link for aluminum alloys that can result in interior or surface-level tears or cracks.
Certain aluminum alloys are more vulnerable to warm splitting than others, and your selection needs to consider this. It can damage both the cast and the die, so you must look for alloys with high anti-soldering residential properties.
Rust resistance, which is currently a remarkable characteristic of aluminum, can vary substantially from alloy to alloy and is an important particular to think about depending upon the environmental conditions your product will certainly be revealed to (aluminum casting company). Wear resistance is one more residential or commercial property commonly sought in light weight aluminum items and can separate some alloys
Report this page